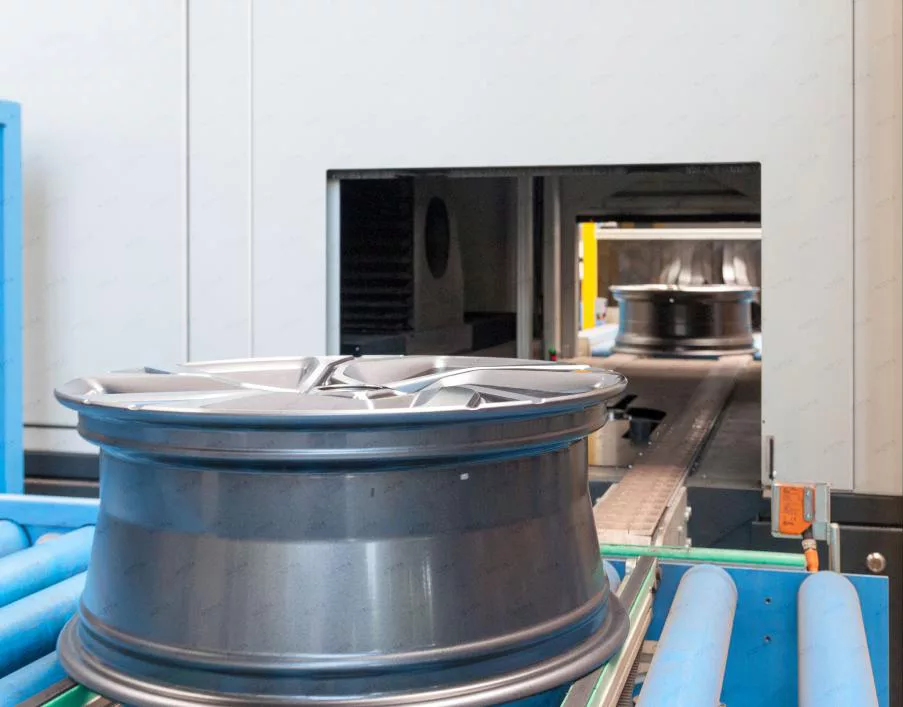
Automated lasering of extravagant wheel designs
In the automotive industry, design and functionality go hand in hand. Find out how Borbet and ACSYS have combined their expertise to redefine the boundaries of wheel design. This success story takes you on a creative and technological journey that led to the development of a customized laser system solution to realize high-quality wheel designs fully automatically.
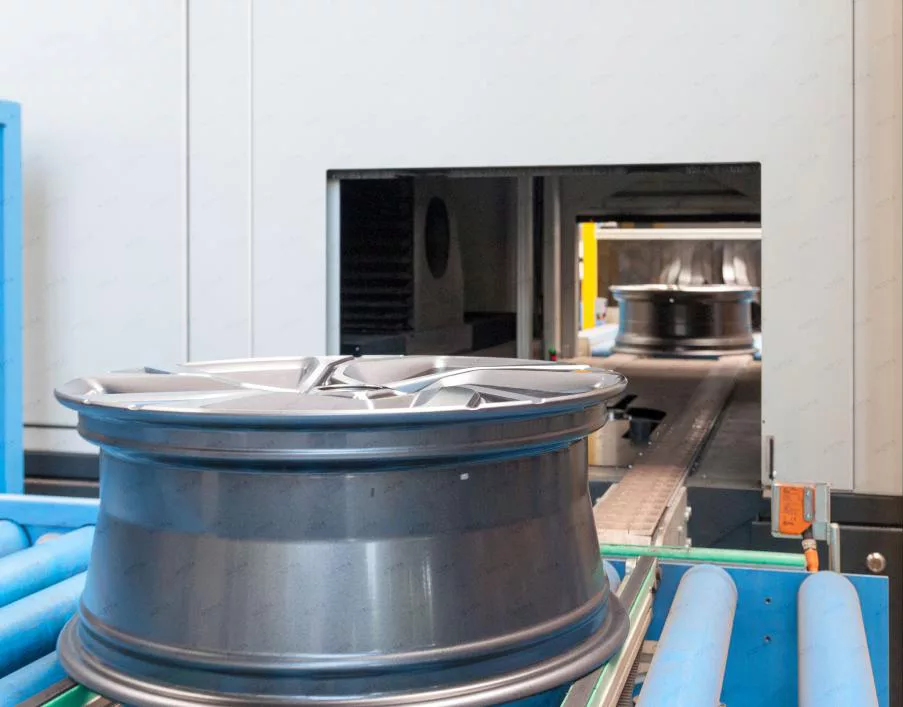
Rich in variants and highly refined
Series production in seven months
Borbet Leichtmetallräder GmbH refines wheel designs in the upmarket wheel segment with partial micrometer-precise material removal. ACSYS has developed a laser system solution consisting of hardware, software and process technology for fully automated production specifically for this purpose and integrated it into the series production process at Borbet in just seven months. The foundation stone for this success story was laid on the one hand by working together as partners and on the other by successfully implementing a pilot project.
A case for the BARRACUDA®
Just 30 weeks passed between the signing of the contract and the start of production at Borbet’s main plant. This was made possible by the modular principle of ACSYS, in which the standard BARRACUDA® system was specifically expanded to meet the process requirements at Borbet and tested at the ACSYS production and development center in Mittweida. “We appreciate the open and honest interaction with the developers and engineers at ACSYS,” says Managing Director Peter W. Borbet, looking back on the constructive collaboration. “We are already familiar with the partnership-based development work from the pilot project for this laser system. Support and service are also running smoothly.” Borbet has been laser cutting various wheel designs on BARRACUDA® laser systems since the end of 2012. However, the system is loaded with alloy wheels manually by an operator. “That’s why there was no question as to who we wanted to implement the new, fully automated process integration with,” emphasizes Peter W. Borbet.
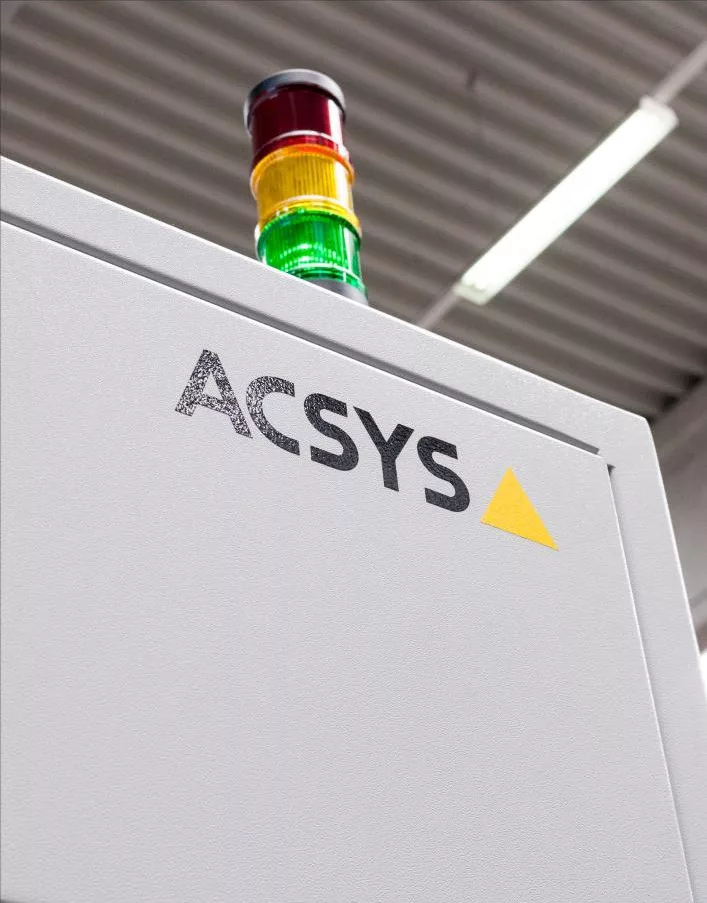
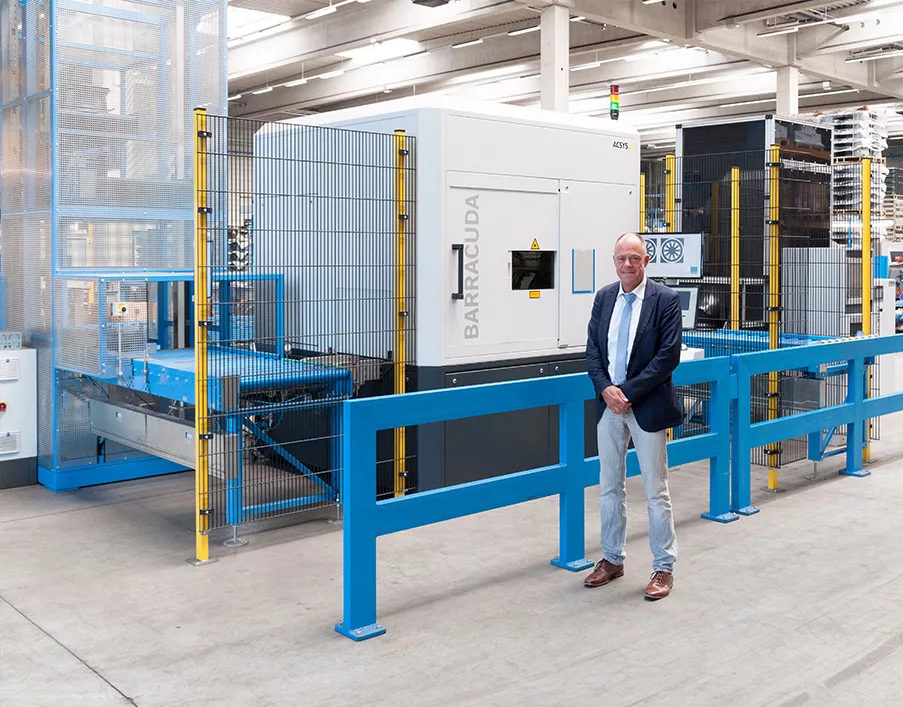
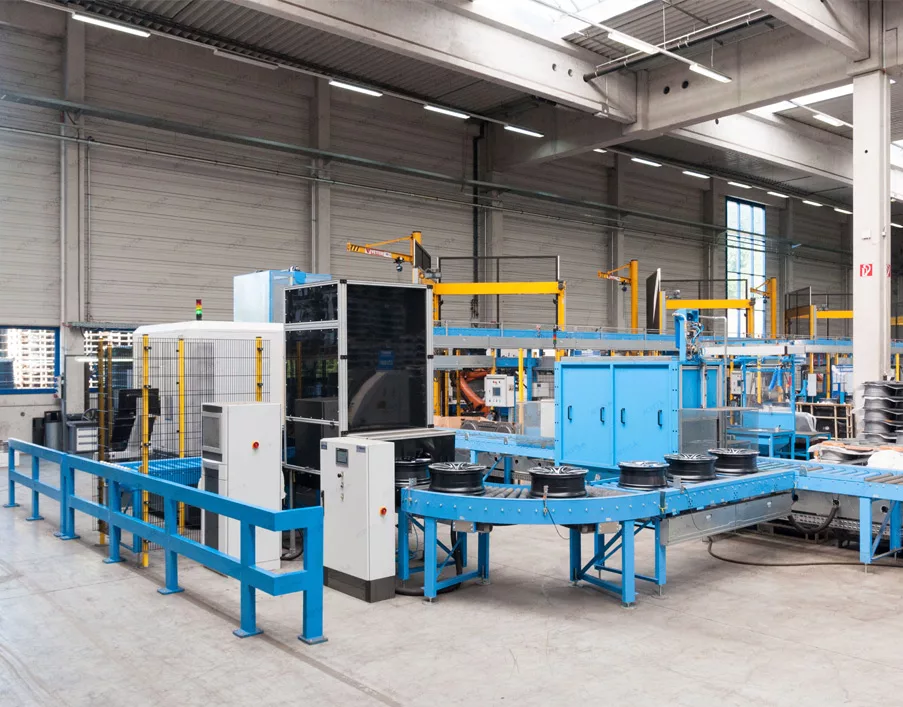
Refined brand quality
Borbet offers over 2,000 design variants of light alloy wheels, some of which are developed in-house from the initial idea to production. Whether winter or summer wheels for off-road or sports cars: the later use of the wheels determines the technical characteristics such as size, weight, bolt circle and wheel loads. The know-how of the manufacturing process – Borbet produces with almost 100 percent vertical integration – is the basis for the designers of the Borbet creative forge.
The specialists design the wheels both for specialist dealer collections and directly for automobile manufacturers (OEMs). The aim of the developers is always to constantly optimize the bike in terms of safety, quality and appearance through innovative manufacturing and production processes. In addition, there is another special feature: with such an emotional brand product, the “external appearance” is a very decisive sales criterion.
The wheels are given their very own “polish” through surface processes such as the application of base coat, gloss turning, matt or colored clear coat and ceramic polishing. For partial paint or aluminum removal, the laser system uses the ExaPeel® process to apply logos, lettering, ornaments and intricate patterns in various colors as a “design finish” before the final clear coat.
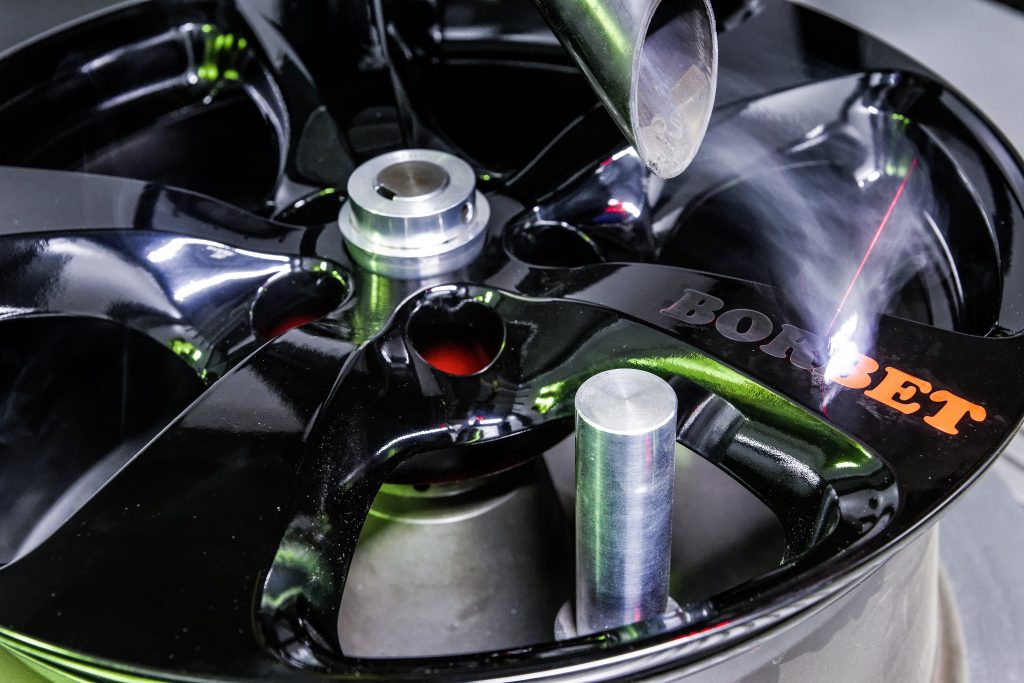
Micrometer-precise paint removal with the laser
Extravagance is based on perfection
The prerequisite for fully automated laser processing is the clear identification and pre-positioning of the wheel. The wheels are produced fully automatically and flexibly, i.e. the wheels arrive at the laser processing stage unsorted according to size, type and laser application. SysCon-Vision GmbH was brought on board to solve this automation task. The company specializes in the detection and implementation of inspection tasks in automated production and in quality assurance using industrial image processing and laser measurement technology. The main challenge was to flexibly design the various wheel shapes, designs and sizes with logos or lettering in series production – without deviations in the micrometer range, because extravagance is based on perfection. The specifications therefore stipulated a number of parameters as unalterable requirements for the laser processing center: wheel type recognition, extremely high positioning accuracy and precise design placement on the wheel surface in the micrometer range. The technical solution was developed jointly by ACSYS, Borbet and SysCon. SysCon supplied hardware and software for wheel detection and pre-positioning. The ACSYS software developers worked very closely with the SysCon specialists on the AC-LASER software interface for data transfer to ensure that all data is processed automatically and in real time by the laser system.
Flexible and yet durable
For the system, Borbet opted for the BARRACUDA® known from the pilot project, which is an all-rounder for automated processing in series production. With a generous, easily accessible work area, this all-rounder offers plenty of space. It was equipped with a low-vibration and temperature-stable granite structure, interchangeable optics and the latest generation of fiber lasers. The design sweeper from SysCon records the wheel type, design and position of the wheel before the laser process, moves the wheel into a defined position, displays the data on a monitor and transfers it to the software of the laser system. Roller conveyors then transport the pre-positioned wheel into the laser chamber of the BARRACUDA®. For laser processing, a fully automatic rotary gripper system aligns the wheel at the exact focus distance in front of the electrically swiveling galvo head to the working position. The galvo head also processes complicated 3D designs in a single operation. The system is equipped with the camera-supported Live Adjustment System (LAS) to display the planned design on the wheel surface. Borbet employees use the 3D assistant integrated into the AC-LASER software to simply upload and store the CAD data of the wheels in the laser system – without any major set-up times for the system.
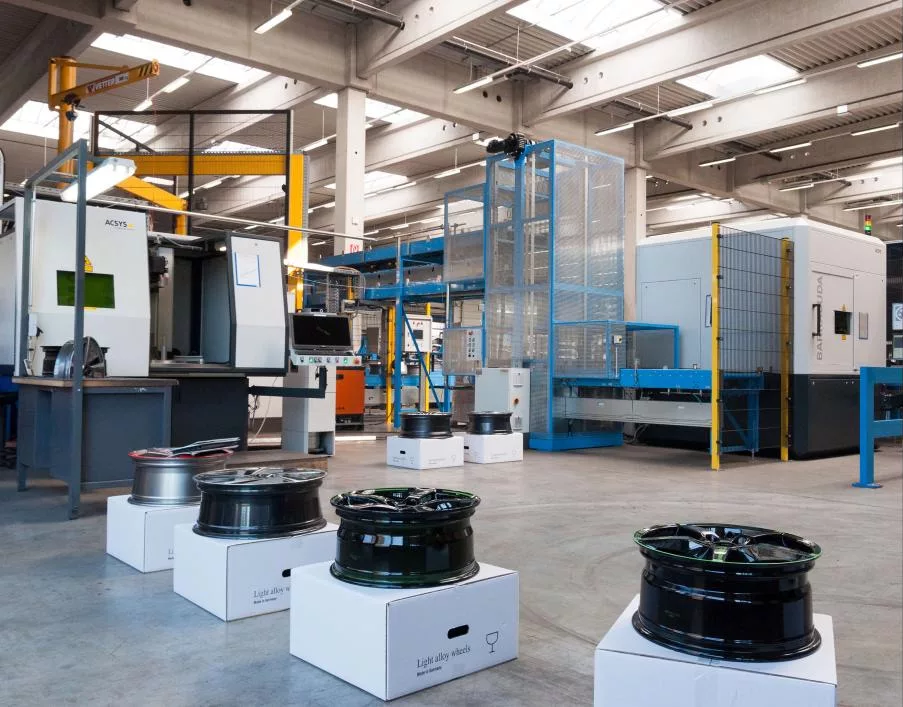
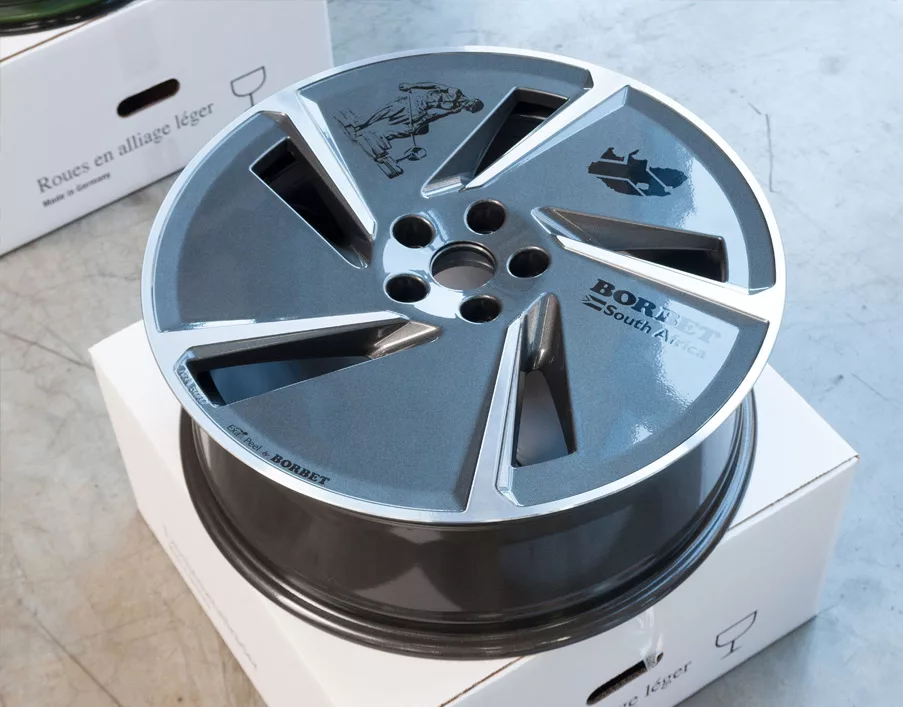
Conclusion
The laser system has been running in a fully automated process at Borbet’s main plant since October 2016. If Peter W. Borbet has his way, the successful cooperation will be extended: “We are very satisfied with the ACSYS laser system and delighted with the constructive cooperation. We are already planning the next ACSYS system in our production facility in Saxony. Further laser system solutions from ACSYS in our other production facilities are already under discussion.”
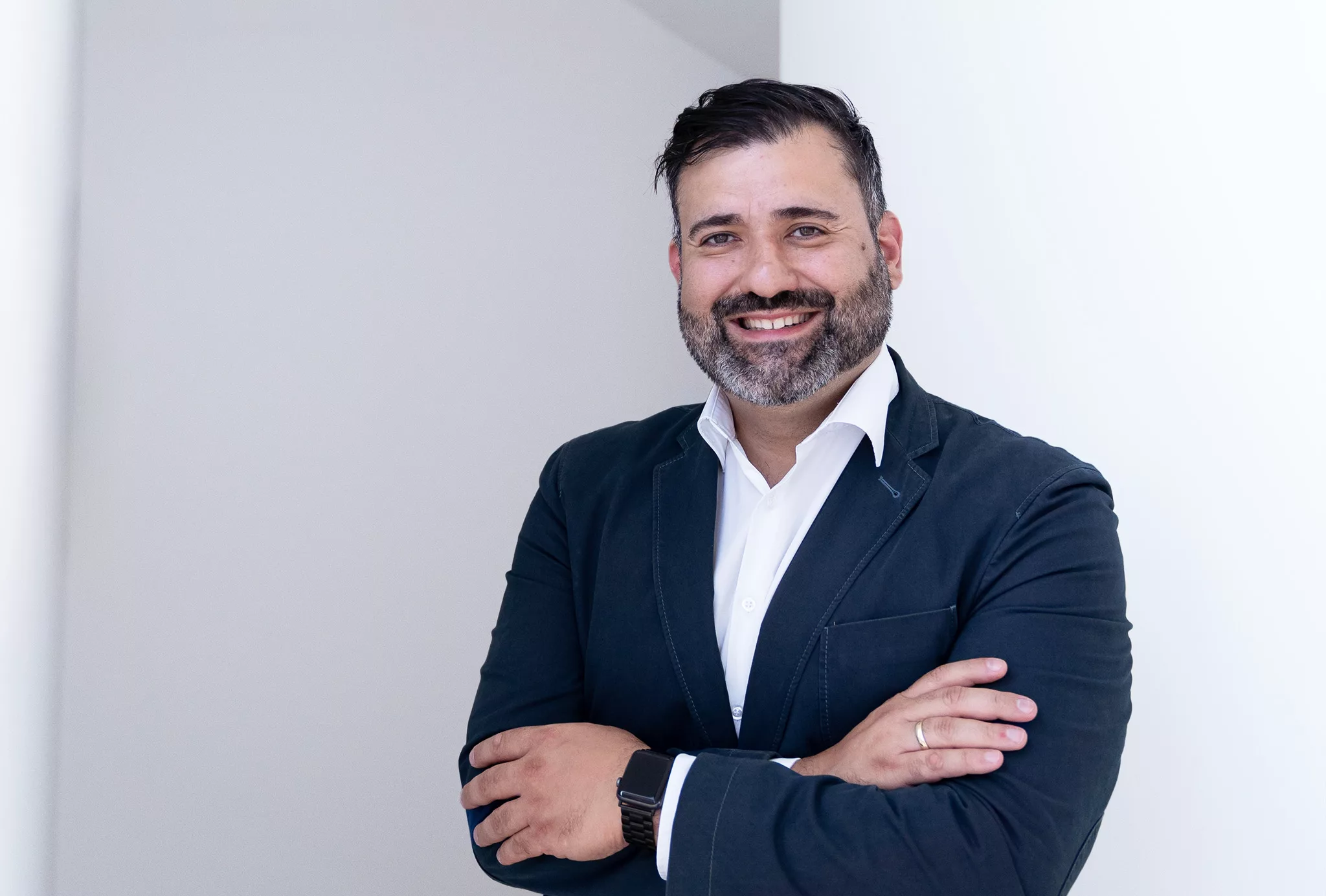
Your ACSYS laser expert
Do you have any questions?
I am happy to help.
Ardalan Masoumi
Business Development Manager
Telephone: +49 7154 80875 531
E-Mail: a.masoumi@acsys.de